Mise en œuvre et bénéfices de la maintenance prédictive des installations industrielles hydrauliques
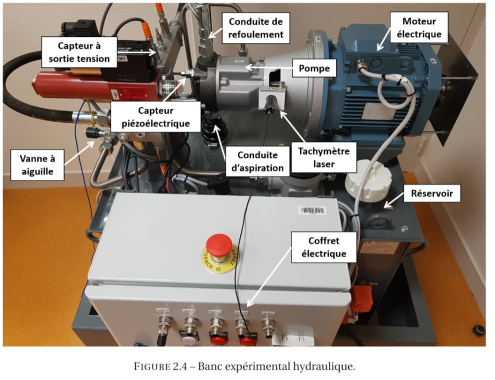
Dans le secteur industriel et sur les installations industrielles hydrauliques notamment, la survenue d’une panne peut avoir des conséquences financières lourdes. Il est heureusement possible de limiter et d’anticiper ces incidents grâce à la maintenance prédictive. Hugo André, Maître de conférences à l’université de Saint-Etienne, nous explique les avantages de la maintenance prédictive et les actions de surveillance à mettre en place.
Maintenance prédictive : anticiper pour mieux protéger
La maintenance prédictive, aussi appelée prévisionnelle, consiste à surveiller finement et de façon répétée les performances d’une installation ou de ses principaux composants afin de limiter les défauts de fonctionnement – ou mieux gérer leur résolution grâce à des opérations de maintenance déclenchées en cas de besoin réel. « Il ne s’agit pas de faire des prédictions, c’est pourquoi je préfère le terme de maintenance prévisionnelle, précise Hugo André. Sur les installations industrielles, on sait que des défauts peuvent se présenter et on sait aussi de quelle manière les prévenir. La maintenance prévisionnelle évalue l’état de santé du système surveillé afin de programmer une action qui permettra d’éviter une panne inopinée. Plus l’impact d’une défaillance est coûteux du point de vue de son exploitation, plus la stratégie de maintenance employée sera complète, technique et proactive ».
La maintenance prévisionnelle est centrée sur l’état de l’installation mais aussi sur sa fiabilité. Dans le cas des installations industrielles hydrauliques (aciérie, levage et manutention, exploitation de gaz de schiste, installations géothermiques…), les systèmes sont complexes. « Certains éléments, particulièrement sensibles, sont à surveiller », explique le chef du département Génie Industriel et Maintenance de l’université de Saint-Etienne :
- Les distributeurs proportionnels : ces éléments sont utiles pour asservir un système à une vitesse ou dans une position donnée. « Ils sont le résultat d’un usinage très fin et la moindre particule présente dans le fluide peut bloquer le système. »
- Les sièges de clapets : utiles pour maintenir le système en position. « L’usure provoquée par le frottement de particules provoque des problèmes d’étanchéité ».
- Les pompes et moteurs hydrauliques : « ils chargent le système et sont sensibles aux particules ou autres problèmes de cavitations », c’est-à-dire aux formations de bulles de gaz.
Dans 70% des pannes des systèmes hydrauliques, la pollution des fluides est en cause. Il convient donc de mettre en place des mesures adaptées aux systèmes afin de limiter au maximum les incidents.
Maintenance prédictive des installations hydrauliques : les points de vigilance
On peut distinguer deux principales applications attribuées aux systèmes hydrauliques. La première est le système de commande hydraulique, en système fermé, qui permet de décupler la force et que l’on retrouve dans de nombreuses industries (BTP, manutention, aciérie…). Dans ce système, le liquide (huile ou eau) est introduit et fonctionne ensuite de manière autonome, sans besoin d’approvisionnement continu. « Cela facilite grandement la surveillance », souligne Hugo André.Dans ces systèmes fermés, on contrôle préventivement la composition du fluide.Trois points sont à étudier :
- La présence de métal dans le liquide ;
- La présence d’eau dans l’huile, qui peut être occasionnée par un joint défaillant et peut provoquer de la corrosion ou de la cavitation (formation de bulles de gaz et de vapeur) ;
- La présence de gaz, due à un problème de cavitation.
Les systèmes de pompage hydraulique, en système ouvert, visent quant à eux à mettre en pression un fluide pour créer un débit dans une direction donnée. « Cela s’applique notamment dans l’industrie lourde qui utilise beaucoup d’eau pour nettoyer ou refroidir, par exemple ». Dans ce type d’installation, le liquide en circulation est renouvelé en permanence. « L’analyse de ce liquide est décorrélée de l’état de santé du système hydraulique. Il sera donc nécessaire de trouver d’autres procédés de surveillance qui reposent sur l’analyse d’autres propriétés physiques telles que la pression instantanée et la vitesse instantanée », résume le Responsable de l'axe traitement du signal pour l'industrie du LASPI de l’université de Saint-Etienne.
Maintenance prédictive : des actions ciblées selon les installations
La maintenance des installations hydrauliques en système fermé se fonde principalement sur l’analyse des fluides lubrifiants. « Cette analyse est le plus souvent manuelle et repose alors sur des prélèvements d’huile périodiques analysés en laboratoire. Il s’agit d’une intervention humaine et donc discontinue », explique Hugo André. Pour un suivi constant et une analyse rapide des résultats, à distance, le recours à un système de surveillance connecté de l’état d’huile (oil condition monitoring) est recommandé. Son intérêt est de fournir directement, en ligne, des informations précises sur l’état des lubrifiants mais également sur le bon fonctionnement des systèmes hydrauliques. Ce suivi permet de planifier un calendrier d’entretien adapté mais aussi de limiter les risques de défaillances.
Pour effectuer la maintenance prédictive des systèmes ouverts, on utilise des capteurs de pression de tendance et des capteurs vibratoires piézoélectriques. Ce dernier, câblé électroniquement à un enregistreur, fonctionne à la manière d’un stéthoscope. « On sait analyser la vibration produite par la machine pour détecter, au travers de son contenu fréquentiel, un comportement défaillant. Récemment, nous avons montré au LASPI que l'étude de la pression instantanée ou de la vitesse instantanée de rotation permet également de détecter de telles anomalies. Nous avons modélisé le comportement d'une pompe et validé expérimentalement que des défauts de pompe (pistons axiaux utilisés dans le BTP, par exemple) pouvaient être diagnostiqués par tous ces moyens. Ces travaux ont été menés au profit d'un industriel actuellement en phase de développement de nouvelles pompes ».
Cette anticipation est un point important : plus la maintenance prévisionnelle est envisagée tôt dans le développement de l’installation, plus elle sera adaptée et donc efficace. On pourra ainsi réfléchir à l'instrumentation de la pompe dès la conception mais aussi limiter les problèmes : manque de place pour le capteur, accessibilité de la pompe (certaines pompes sont enfouies), évaluation erronée de l'état initial de la machine.
Les bénéfices concrets de la maintenance prédictive
Pour les installations industrielles hydrauliques, les stratégies de maintenance prévisionnelles sont vivement conseillées pour la sécurité des équipes et pour l’optimisation financières des équipements. « C’est une erreur d’imaginer que l’on va uniquement gagner sur le prix de l’élément que l’on protège et qui est finalement peu élevé au regard des pertes de production. La maintenance prévisionnelle permet en réalité d’optimiser le temps de production : plus on se fait surprendre par une panne et plus le temps d’arrêt risque d’être long avec plus d’équipements impactés, des délais de livraison plus longs et incompressibles… » résume Hugo André.
La maintenance prédictive limite donc les pannes et les pertes financières qui leur sont liées. Elle augmente la durée de vie des équipements et leur temps de fonctionnement en permettant de planifier les interventions de maintenance réellement nécessaires. Un investissement qui contribue en outre à réduire les coûts de maintenance curative.
Nos autres actualités
Tout voirRejoignez la plus grande communauté de fournisseurs industriels
- Vous aider dans votre veille technologique permanente
- Vous offrir des statistiques fournisseurs détaillées
- Vous offrir une visibilité à l’internationnal
Découvrez le plus grand catalogue de produits industriels du marché
- Vous offrir le meilleur catalogue de produits industriels du marché
- Vous garantir une plateforme 100% sécurisée
- Vous permettre des échanges à distance en direct