AGC BUSINESS CONSULTING SA
Shell foundry parts
Looking for the ideal supplier for the production of your shell foundry parts? AGC , with 20 years of experience in the field, offers you its expertise for solutions at low-cost tooling prices , very low foundry costs and very competitive finishing (deburring, machining, surface treatment, packaging)
Shell foundry makes it possible to optimize the production of precision parts in small and medium series. We offer you to make your parts in order to benefit from the lowest costs while maintaining a guarantee on the quality. Send us the details of the parts you want to make, we will send you a tooling + parts offer delivered on site very quickly.
Our shell foundry capabilities
- Pieces from one hundred grams to several tens of kilograms
- Subjects offered:
- Aluminum
- Magnesium
- Zamac
- Possibility of anodizing
- 3 and 4 axis machining centers
- Assembly possibilities
WHAT IS SHELL FOUNDRY?
Shell casting, also called steel mold gravity casting, is a technique for producing metal parts by pouring molten material into a steel mould. The metal hardens as it cools and conforms to the shape of the mold cavity. It is possible to add cores and pins to create voids and internal shapes in the part. The casting process can be done manually or automatically via a ladle or crucible from above the mould. The mold is then opened in two along the parting line to extract the parts. It should be noted that a liquid is added to the walls of the mold (coating) in order to facilitate demoulding.
The applications are very numerous from industry to the manufacture of decorative elements.
ADVANTAGES OF SHELL FOUNDRY
- Die casting requires much less investment than pressure die casting in both tooling and equipment
- The permanence of the mold allows better repeatability than sand or lost wax casting as well as better performance.
- Better surface finish and precision than other gravity casting methods
- As the mold is made of metal, there is better thermal conductivity than sand or lost wax tools and therefore faster and better distributed heat loss.
DISADVANTAGES OF SHELL FOUNDRY
- Higher tooling cost than sand or lost wax casting
- Presence of a joint surface to be deburred
- Need for heat treatment to release internal stress
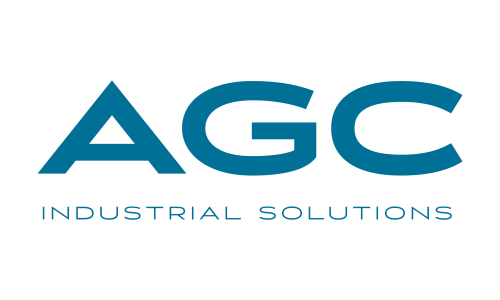