Achieving optimum performance through improved lubrication practices
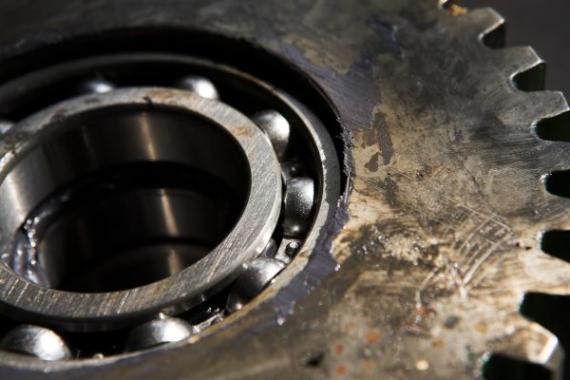
Manufacturers increasingly recognize and accept that lubrication is the cornerstone of reliable machine operation. Yet understanding the intricacies of why and how lubrication is done remains a challenge for many. The question “Why lubricate?” may seem simple, but the answers vary and reveal the complexity of this essential practice.
Why do we lubricate?
When asked why lubrication is necessary, the most common answers are “to combat friction” and “to reduce heat.” While these answers are accurate, they barely scratch the surface of the issue. The primary reason for lubrication is to create separation between moving surfaces, preventing direct contact that leads to wear and failure. This principle applies not only to engine bearings, but also to pistons, chains, gears, and linear bearings. Proper lubrication ensures that these surfaces remain separated, reducing friction, wear, heat, and energy consumption.
Lubricants, especially greases, also provide other benefits such as corrosion control.
Additives in greases can prevent rust and protect moving parts from contaminants, provided the grease is applied and stored properly. Although lubrication science has evolved over the millennia, the fundamental goal remains the same: maintain separation to extend asset reliability.
Understanding Fat and Its Properties
The science behind grease formulation is complex and tailored to a variety of applications. Grease is comprised of a base oil, a thickener, and additives. The base oil forms the hydrodynamic film that separates the metal components, providing functional separation. Thickeners hold the base oil in place, allowing the grease to perform effectively regardless of machine orientation, while additives improve lubricity, combat oxidation, and withstand extreme pressures. However, additives degrade over time, making accurate lubrication intervals critical.
Demystifying lubrication
Misconceptions about grease often lead to poor practices. Over-greasing is a common mistake, leading to increased friction and heat, while under-greasing does not adequately protect components. Contrary to popular belief, more grease does not equal better cooling. Bearings need air space to dissipate heat. Additionally, not all bearings with grease fittings need to be greased; some are designed to be “sealed for life.”
Effective lubrication requires a balanced approach, not excess grease. Over-greasing can force the thickener into the bearing “war zone,” leading to premature lubricant degradation and viscosity change. The goal is to move bearings from the kneading phase, where the thickener is present, to the bleeding phase, where only the base oil lubricates the contact points, minimizing friction and wear.
Connection with LUBExpert
LUBExpert’s sophisticated ultrasonic technology monitors friction levels and provides precise feedback during the lubrication process. This ensures that bearings receive the exact amount of grease needed at the correct intervals, eliminating the guesswork that often leads to over- or under-lubrication. By monitoring bearing health, LUBExpert helps prevent premature failure and extends the life of critical assets.
Features and benefits of LUBExpert:
- Bearing Database: LUBExpert maintains a comprehensive database of all your assets, including bearing types and dimensions. This allows for tailor-made lubrication strategies to be developed for each asset, ensuring optimum performance and longevity.
- Automation: The system automates the calculation of settling time between grease pumps, eliminating guesswork and ensuring consistency in lubrication practices.
- Guided and Free Modes: Whether your lubrication program is well established or just starting out, LUBExpert offers Guided and Free Modes to meet your needs. Guided Mode provides step-by-step instructions, while Free Mode allows experienced technicians to work with more flexibility.
- Shopping Lists and Work Orders: LUBExpert simplifies daily tasks by generating “shopping lists” for the right type of grease and the right amount needed. It also creates work orders, reminding technicians which bearings need to be lubricated, restoring discipline to your maintenance program.
- System Messaging: The system documents and communicates the reasons why assets were omitted, ensuring transparency and continuous improvement of lubrication practices.
- Dynamic Option: The LUBExpert Dynamic Option connects the lubrication team with the condition monitoring team. This integration allows for the collection and analysis of dynamic data, filling information gaps and improving overall asset management.
On the road to better lubrication
By switching to LUBExpert, companies can move from reactive, time-based lubrication practices to proactive, condition-based strategies. This shift not only reduces the risk of bearing failure, but also optimizes energy consumption and operational efficiency.
Training and proper use of tools are essential to achieve lubrication excellence. The LUBExpert provides lubrication technicians with the data and guidance needed to perform their tasks accurately, transforming them into true LUBExperts themselves.
Lubrication is more than just adding grease to moving parts. It’s about understanding the science behind it and applying that knowledge to achieve optimum performance. With LUBExpert, you can improve your lubrication practices and ensure your machines run smoothly and reliably.
Our other news
See allJoin the largest community of industrial suppliers
- Helping you with your ongoing technology watch
- Provide you with detailed supplier statistics
- Give you international visibility
Discover the largest catalogue of industrial products on the market
- To offer you the best catalogue of industrial products on the market
- To guarantee you a 100% secure platform
- Enable you to have live remote exchanges