SDT Ultrasound Solutions unveils the CRY8120 Series Acoustic Imaging Camera
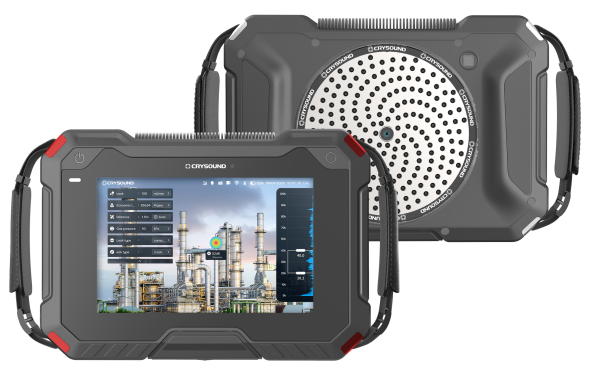
SDT Ultrasound Solutions is thrilled to announce the launch of the highly anticipated CRY8120 Series Acoustic Imaging Camera, designed by CRYSOUND. This state-of-the-art device represents a significant leap forward in industrial inspection technology, offering unparalleled precision, personalization, and performance.
Benoit DEGRAEVE, CEO of SDT International, commented, “We are incredibly proud and honored to represent this cutting-edge technology. Our common commitment and dynamism allow us to offer innovative solutions that not only meet the current needs of our customers but also define the future of the industry. Together, we have the chance to advocate for and promote technology that is not only state-of-the-art but also designed to be robust, adaptable, and sustainable in demanding industrial conditions. The CRY8120 Series is not just a camera; it is a concentration of innovation embodying precision, personalization, and performance.”
Raising performance standards
The CRY8120 Series, encompassing models CRY8124 and the forthcoming CRY8125 (IECEx version), is engineered to set new benchmarks in accuracy and efficiency. Leveraging cutting-edge ultrasound, vibration, and temperature sensor technology, this series ensures superior detection and analysis capabilities across a wide frequency range (2 kHz to 100 kHz). The advanced 200-channel MEMS microphone array provides unprecedented precision in identifying gas leaks, electrical discharges, and mechanical faults, even from greater distances.
Innovative features and user-centric design
The CRY8120 Series is designed with the user in mind, featuring an 8-inch (1920 x 1200) high-resolution touchscreen display with 600 nits brightness that offers an intuitive and seamless experience. Customizable templates allow users to create tailored workflows, integrating PRPD spectrograms, time domain charts, thermal images, and more.
A key differentiator of the CRY8120 Series is the new attachable thermal camera module. This optional module enhances the device’s capabilities, allowing for comprehensive inspections by integrating thermal imaging with acoustic detection. Users can easily switch between ultrasound and infrared data, presenting a multidimensional view of the inspection area. The thermal image can be dragged to different areas of the main screen for split-screen or thermal view mode, providing a more detailed analysis of potential issues.
Commitment to sustainability and efficiency
In addition to its high-performance capabilities, the CRY8120 Series is designed to support green initiatives by pinpointing and mitigating energy losses, thus optimizing resource usage. The energy-efficient design, combined with a removable battery system that provides up to 5 hours of continuous use, ensures minimal power consumption and lower operational costs. With an optional second battery, users can get up to 10 hours of continuous operation.
Seamless connectivity and comprehensive software tools
Equipped with Bluetooth and Wi-Fi, the CRY8120 Series facilitates easy data transmission and remote report generation. The comprehensive software suite includes tools for multi-point imaging, directional focus, distance measurement, and detailed report exports, streamlining the inspection process and enhancing overall productivity.
The CRYSOUND’s exceptional capabilities are a testament to its remarkable engineering and design, and we believe that it will even further transform the way industries approach maintenance, offering improved accuracy, efficiency, and versatility.
About SDT Ultrasound Solutions
SDT Ultrasound Solutions is a leading provider of ultrasound technology and services, committed to delivering innovative solutions that enhance the reliability and efficiency of industrial assets.
About CRYSOUND
CRYSOUND specializes in the development of advanced acoustic imaging and sensor technology. With a focus on innovation and quality, CRYSOUND is dedicated to providing cutting-edge solutions that meet the evolving needs of various industries.
More info at https://sdtultrasound.com/products/crysound/cry8120/
Our other news
See allJoin the largest community of industrial suppliers
- Helping you with your ongoing technology watch
- Provide you with detailed supplier statistics
- Give you international visibility
Discover the largest catalogue of industrial products on the market
- To offer you the best catalogue of industrial products on the market
- To guarantee you a 100% secure platform
- Enable you to have live remote exchanges