Four reasons why we condemn our industrial air compressors to an early death
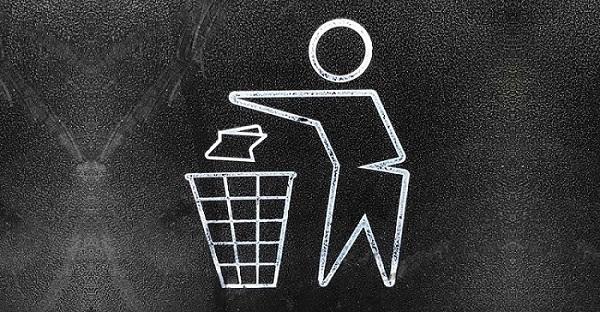
Compressors are some of the most heavily used equipment in a factory and must operate tirelessly, day in and day out, to meet the demand for compressed air needed for production. Their use is so common that most factories require multiple compressors to meet demand. What is often forgotten is that in addition to the compressed air needed for production, there is a significant artificial demand for this resource. An artificial, invisible demand that destroys production efficiency and factory sustainability, while eating into company profits.
Up to 30-40% of compressed air is completely wasted. When a compressed air system suffers from leaks, it is the compressors which are forced to take over and when they must operate beyond their operating time to cover the artificial demand caused by the leaks. air, they are subject to greater wear. All of this leads to unplanned breakdowns and excessive workload for maintenance teams.
Constant overuse of an industrial air compressor has a compounding effect on the deterioration of its reliability. Although this phenomenon can be compensated for by regular compressor maintenance (often a maintenance team's first or only course of action), routine compressed air leak checks performed using a Ultrasonic leak detector are much more effective in reducing the workload of an air compressor and, therefore, extending its lifespan.
The main reason an industrial air compressor is scrapped is the burden of a leaking compressed air system. SDT has repeatedly seen neglected and leaking compressed air systems, which highlights several glaring cultural and ideological problems common to the manufacturing industry worldwide. The following list summarizes the four reasons why a compressed air system fails, forcing the compressor to suffer the consequences and make the ultimate sacrifice.
1. The compressor is not highly ranked in a plant's strategic equipment management plan
Industrial air compressors sometimes end up decoupled from production. Whether it's because they are in a room, far from the production line, or for any other reason... But as a result, they find themselves low on the maintenance teams' priority list and, in some cases, the maintenance task of an industrial air compressor is entrusted to a third party.
Compressor manufacturers can take care of their maintenance in factories, and in this case, when the maintenance and reliability of equipment is outsourced, a maintenance team can separate itself from that equipment. Falling out of the maintenance team's maintenance schedule results in equipment and its components being forgotten, which can extend to compressed air lines, pipe fittings, etc. .
2. Lack of understanding regarding the sustainable and fiscal results of an inefficient compressed air system
The cost associated with manufacturing compressed air is often overlooked, which can lead to rather frivolous uses of this expensive resource. By the time the air is compressed, cooled and dried, then regulated and transported to its point of use, significant costs have been incurred. Only about 15% of the electricity consumed by the compressor is used to transport the compressed air to its point of use. The remaining 85% is lost due to heat released by air compression. This astonishing figure of electricity consumed for this resource becomes even more staggering when you take into account the amount lost to leaks. Considering that even with a leaky compressed air system, most factories can continue production without too many problems, it is not surprising that the costs associated with air compression can add up to more than of 30% of a manufacturer's electricity bill.
A corporate culture that tolerates this waste does not do so out of malice. Rather, it is a misunderstanding of the costs, the adverse environmental effects, or the fact that the system is leaking. This promotes poor use of the resource and, more importantly, downplays the importance of maintaining a healthy compressed air system.
3. Compressed air systems give little indication of leaks and difficulty meeting demand
Leaks from a compressed air system are not always visible. This is, in the truest sense of the term, a hidden cost. Of course, standing in the middle of a factory during a maintenance shutdown would reveal hundreds of whistling compressed air leaks. And if enough time is spent, some of them might even be located and repaired. But that's not a luxury many maintenance teams can afford. What happens when the machines are running at full capacity and production is in full swing? Under these circumstances, compressed air leaks cannot be heard or seen. They pose no risk to the health and safety of plant workers, and their only real threat to production is the imminent failure of an overloaded compressor.
4. Searching for compressed air leaks takes time and effort
Searching for compressed air leaks in a large factory can be a time-consuming and tedious job. In a facility, there are hundreds of meters (or more) of compressed air lines, rubber hoses, and piles of other components that make up a compressed air system. All of these components can leak, harming system pressure, plant durability and profits.
Keeping all of this under control can seem like a daunting task. However, with the help of an ultrasonic leak detector or acoustic imaging camera, finding and repairing leaks becomes much simpler. Ultrasound can locate leaks that would otherwise be impossible to detect in a noisy factory. An acoustic imaging camera like the CRYSOUND goes even further by using its ultrasound detection capabilities coupled with its camera to detect leaks and make them visible on its display screen. The CRYSOUND can mark leaks by taking a photo or leak points during inspection, making locating, documenting and repairing leaks easier than ever.
Our other news
See allJoin the largest community of industrial suppliers
- Helping you with your ongoing technology watch
- Provide you with detailed supplier statistics
- Give you international visibility
Discover the largest catalogue of industrial products on the market
- To offer you the best catalogue of industrial products on the market
- To guarantee you a 100% secure platform
- Enable you to have live remote exchanges