NORELEM
plastic guide
Eccentric Forces
Certain recommendations should be taken into account when using DryLin maintenance-free linear plain bearings. Since the coefficient of friction is higher than on ball guides, a greater driving force should be provided. To optimize sliding and reduce wear, the bearings should be as far apart as possible and the torque created by the load should be as low as possible.
Quiet operation
Plastic sliding elements running on polished shafts or profiled rails generate almost no noise. Unlike traditional ball guides, the noise level does not rise as the speed increases.
The 2:1 rule
Failure to follow the 2:1 rule when using linear plain bearings will result in erratic movements or even system jamming. Often, relatively simple modifications can remedy the problems. This principle is not a function of load or driving force. It is produced by friction and always refers to the fixed bearing.
The further the drive is from the guide bearing, the greater the wear and the required driving force. A gap between the driving force and the fixed bearing twice as large as the gap between the bearings (rule 2:1) theoretically results in a jamming of the guide and a coefficient of friction when tearing out of 0.25.
Design Guidelines
When using systems with two parallel rails, one side must be designed as a floating bearing. For every mounting position, horizontal, vertical or lateral, there is the appropriate fixed/free bearing solution. This mounting method prevents the guide from seizing or jamming in the event of a deviation from parallelism between the rails.
The free landing is achieved by moving the hyperstatic sliding elements away. This therefore results in an additional degree of freedom in the direction of the probable lack of parallelism on a rail. Compensation for lack of parallelism between the mounted rails is possible within a range of 0.5 mm maximum in the case of a fixed/free bearing. When mounting, ensure that the free bearing has the same amount of play in both directions. The models of fixed/free bearing systems that we recommend are shown in the diagram opposite.
The connecting surfaces for the guide rails and carriages must have a good flatness (eg milled surface) in order to avoid the risk of warping in the system. Small irregularities in the mating surfaces can be evened out individually up to a certain point (0.5 mm) using a larger preset clearance. Clearance adjustment is effective only when no load is present.
- DryLin® T guide carriage - DryLin® T guide rail - DryLin® T miniature guide - DryLin® N miniature guide - DryLin® N miniature guides - DryLin® N miniature guide - DryLin® N linear guide - DryLin® guide carriage W - DryLin® slider W - DryLin® guide rail W single - DryLin® guide rail W double
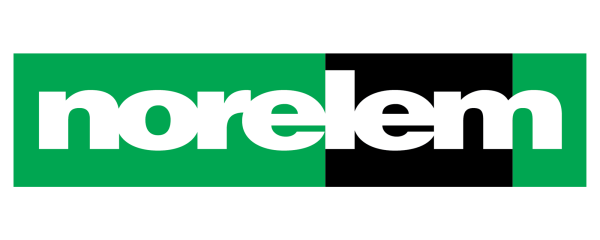