When and why truncate the tip of the tungsten electrode?
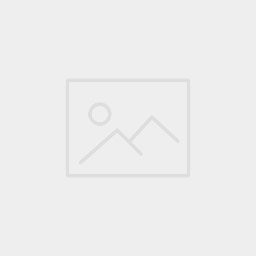
There are two situations when doing TIG welding that really wear down the tungsten electrode.
1. High current welding
2. Welding aluminum with alternating current
The first situation affects the tungsten electrode because the arc generates a lot of heat. Despite the fact that tungsten has a melting temperature of 3422°C (=6192°F), it is still affected by heat like other metals. In other words, the thinner the material, the less heat it can tolerate. On a sharp electrode, the tip cannot withstand the same heat as the body of the electrode. Therefore, welding at high current wears the tungsten electrode more because it generates more heat than at low current. In the worst case, the tip of the tungsten electrode melts, falls into the weld pool and contaminates the weld.
The second situation, when an alternating current is used, for welding aluminum for example, the alternation of polarity also exerts a stress on the tungsten electrode. In alternating current welding, the heat is alternately concentrated on the electrode and on the base material. This leads to the electrode melting and forming a large "ball". With the wrong settings, sharp or not, the electrode tip will melt improperly and form a large "ball", resulting in an unstable, flickering arc, a wide weld bead, and poor weld quality.
On the other hand, with the right settings (frequency, AC-T and AC-I balance and electrode preheating), you can pretty much keep the electrode tip sharp. However, if the electrode is sharpened too sharp, it will melt due to too much heat being generated. In this case, the risk of the tip falling into the weld pool and contaminating the solder is higher.
In both situations, the risk of tip melting can be reduced by performing truncation. Experiments have shown that with a truncated electrode, melting of the tip is avoided and its geometry is maintained, which gives a stable arc AND a greater longevity of the electrode, therefore more welding time before a resharpening is necessary.
Conclusion:
Sharpen the electrode with a truncation when performing high current welding or AC welding!
Because it allows:
- Better welding quality
- A more stable arc
- Less electrode wear
Our other news
See allJoin the largest community of industrial suppliers
- Helping you with your ongoing technology watch
- Provide you with detailed supplier statistics
- Give you international visibility
Discover the largest catalogue of industrial products on the market
- To offer you the best catalogue of industrial products on the market
- To guarantee you a 100% secure platform
- Enable you to have live remote exchanges