When to measure the bolt tension of a bolted assembly?
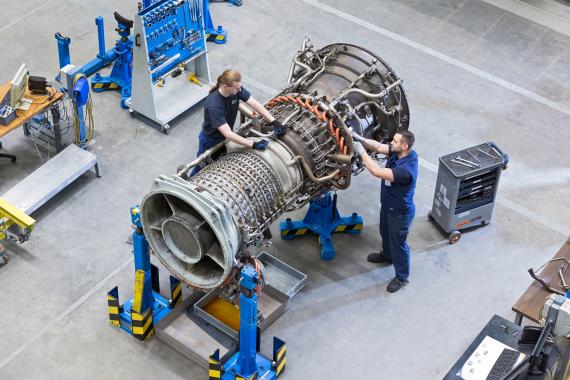
This article aims to list various applications enabled by bolt load measurement, covering design, assembly, maintenance and detection of tightening-related anomalies.
New perspectives in the industry
The concept of bolt tension tightening, already adopted by the big names in global industry, is in full expansion. It has already proven itself in sectors such as automotive, aeronautics, energy and transport. In addition to the obvious improvements in performance and precision, this method opens up new possibilities in the field of tightening. For example, it is now possible to follow the evolution of the tightening of an assembly over time and to monitor the behavior of screwed assemblies in real time. In the long term, it also becomes easy in maintenance to check the condition of a bolted assembly over several years. This conceptual advance leads to the emergence of innovative applications and transforms the way in which assemblies are designed and produced in factories.
During the design phase
1- Perfect the design of the assemblies
During assembly, the use of these same systems makes it possible to check whether the tension applied between the parts corresponds to that defined by the design teams.
2- Reduce prototyping time
Designing an assembly prototype often requires a lot of trial and error. Let's take the example of studying a new cylinder head gasket: its behavior is closely linked to the tension of the cylinder head studs. When torqueing, it is difficult to differentiate the effects of the tightening from those of the joint itself. You must perform multiple tests to characterize the behavior of the joint, statistically eliminating variations due to tightening.
On the other hand, controlling the tightening tension makes it possible to study the behavior of the joint independently of tightening variations. By controlling the voltage, it becomes possible to separate these two variables, thus simplifying the study by reducing the number of parameters to consider.
During assembly
1- Controlling installed tension between components
A threaded assembly is secured by a cohesive force between its components, corresponding to the tension applied to the bolts that join the assembly. Tension measurement devices operate independently of the tool used to tighten the bolts (whether it's a screwdriver, torque wrench, or hydraulic tensioner). Users of these devices synchronize their tightening process with tension measurement: during tightening, regardless of the tool used, they directly monitor the tension evolution on the measurement device.
2- Ensuring optimal seal of joints and applying uniform tension between assembled parts
Since joints play a crucial role in assembly sealing, the bolts used to maintain pressure on the joint can either ensure a tight seal or compromise it if tension isn’t uniformly distributed across the joint surface. Given the sensitivity of joints to pressure, using a tension measurement system to apply uniform tension between parts ensures adequate assembly sealing.
During maintenance
1- Monitoring assembly quality by controlling tension installed by robotic tightening systems
How do you determine if screwdrivers on a production line achieve the predefined tightening tension and maintain it consistently over time? With a bolt tension measurement device, it's possible to statistically verify if screwdriver setting parameters (torque/angle) achieve controlled tensions. It also enables adjustment of settings to achieve "acceptable" clamping tensions in production, as done at Stellantis, for example.
2- Monitoring long-term assembly behavior
In industries like refineries or wind energy, maintenance of bolted assemblies often involves complete disassembly and reassembly, accounting for about 20% of bolted assemblies annually in the wind sector alone. This process is cumbersome, repetitive, and outdated.
Another method, known as torque re-tightening, involves slightly loosening the assembly before re-tightening. However, during re-tightening, operators may inadvertently apply higher tension than initially intended, risking exceeding the bolt's elastic limit and causing deformation.
Regardless of the method used, maintenance is significantly more reliable and streamlined with a clamping tension measurement device. These non-intrusive systems allow tension measurement between two parts simply by measuring the bolts in the assembly. Thus, it's possible to monitor bolt tension over time (spanning from a month to five or twenty years). By comparing initial tightening data with subsequent measurements, such as during the first maintenance cycle, it's easy to detect loosening or anomalies in the assembly. This method proves highly effective for long-term control, monitoring, and surveillance of assemblies.
Anomaly Detection
1- Investigating tightening incidents through controlled disassembly
It's common to suspect a loss of tension in one or more bolts. A typical method to verify this involves measuring the bolt tension of suspected bolts before disassembly to determine their residual tension. Comparing this tension with the theoretically expected value helps determine if there has been any relaxation and to what extent. This information then initiates an investigation to identify the causes of loosening.
Our other news
See allJoin the largest community of industrial suppliers
- Helping you with your ongoing technology watch
- Provide you with detailed supplier statistics
- Give you international visibility
Discover the largest catalogue of industrial products on the market
- To offer you the best catalogue of industrial products on the market
- To guarantee you a 100% secure platform
- Enable you to have live remote exchanges