The SDT340: A complete solution for equipment reliability
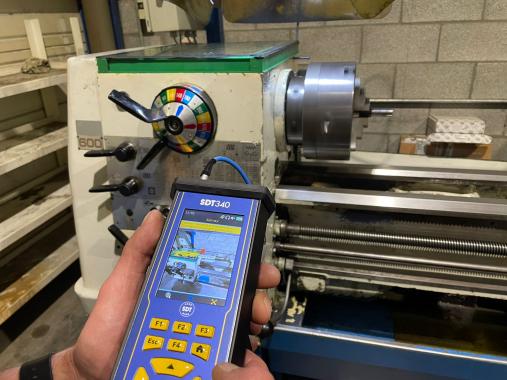
In industrial operations, maintaining the health and functionality of assets is central to flawless productivity.
That’s where ultrasound technology changes the game, offering a versatile and effective way to detect and treat potential problems before they arise. In this article, we explore the importance of ultrasound inspections, focusing particularly on the advanced capabilities of the SDT340 ultrasound detection device.
Ultrasound technology enables operators to play an integral role in asset reliability. Simple tasks such as finding leaks, inspecting shaft couplings and testing steam traps can be performed effortlessly by operators with minimal training. This approach not only capitalizes on operators’ familiarity with the assets, but also reduces energy wastage and minimizes unplanned emergency maintenance interventions.
The need for ultrasound in noisy environments
Manufacturing environments are notoriously noisy, making it difficult to detect subtle defects with the naked ear. Ultrasound detectors, such as the SDT340, cut through the noise and identify defects that would otherwise go unnoticed. Its ability to identify faults earlier than other condition monitoring technologies makes it a valuable tool in predictive maintenance strategies.
The detector in detail
The SDT340 is an ultrasound and vibration data collector designed to detect and analyze ultrasound and vibration data from a variety of industrial equipment, providing an all-in-one solution for comprehensive condition monitoring.
It stands out not only for its advanced capabilities, but also for its meticulously designed features that redefine asset reliability management.
One of the most remarkable features of the SDT340 is its compatibility with the Ultranalysis® Suite 3 (UAS3) software. This integration facilitates the streamlining process for users, enabling them to effortlessly download and organize inspection results. The UAS3 software is not only a data repository, but also gives users the ability to customize their condition monitoring strategies, tailoring the approach to the unique needs of their industrial equipment.
One of the outstanding features of the SDT340 is its information screen, which gives users direct access to crucial information. This includes images of the machine to be inspected, specific examination points and required sensors, all imported seamlessly from the UAS3 software. This intuitive design improves the efficiency of field inspections, enabling operators to access vital data without unnecessary delay.
The SDT340 takes user-friendliness to a new level, thanks to its well-thought-out design. The device is designed to simplify the inspection process, eliminating the risk of measurement errors due to memory gaps. The emphasis on ease of use ensures that operators can navigate the device with ease, improving overall inspection efficiency.
Durability is the cornerstone of the SDT340’s design. Designed to withstand the rigors of industrial environments, the device features an extruded aluminum housing protected by shockproof rubber. This rugged construction ensures that the SDT340 can withstand the bumps and knocks of daily use, providing operators with a reliable tool that stands up to the challenges of the field. For added protection against dust and wear, users can opt for the durable nylon case, which demonstrates the unit’s commitment to longevity and long-lasting performance.
The SDT340’s High Signal Resolution (HSR) feature sets it apart in terms of accuracy. This unique feature increases sampling rate and sensitivity, enabling users to detect even the most difficult defects with confidence.
The eight pillars
SDT identifies eight areas, “the eight pillars of ultrasound”, in which ultrasound and the SDT340 are essential for ensuring asset reliability:
- Mechanical condition monitoring: Early detection of bearing faults to prevent unexpected failures.
- Bearing lubrication monitoring: Ensure that the right amount of lubricant is applied at the right intervals.
- Compressed air and gas leak detection: Locate air leaks to reduce energy consumption and maximize uptime.
- Electrical equipment fault detection: Safe inspection of electrical systems using ultrasound.
- Steam trap testing and maintenance: Keep steam systems clean, safe and energy-efficient.
- Valve condition monitoring: Check that valves are closed properly.
- Hydraulic system monitoring: Detect leaks, bypasses and blockages in hydraulic systems.
- Tightness testing: Ensuring the tightness of enclosed spaces to save energy and money, protect against the elements and respect the environment.
Our other news
See allJoin the largest community of industrial suppliers
- Helping you with your ongoing technology watch
- Provide you with detailed supplier statistics
- Give you international visibility
Discover the largest catalogue of industrial products on the market
- To offer you the best catalogue of industrial products on the market
- To guarantee you a 100% secure platform
- Enable you to have live remote exchanges