Steam Traps and Valves: Leveraging the SDT340 for Predictive Maintenance and Energy Efficiency
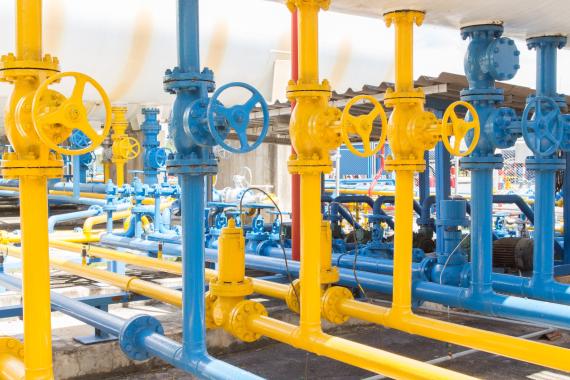
Energy efficiency and system reliability are so important for industries that rely on steam systems and valves, from manufacturing to oil and gas production.
These components play a huge role in maintaining optimal operational conditions, reducing waste, and ensuring safety. But sometimes, manufacturers don’t have the proper tools to address their potential failures, or don’t even know that some exist.
Silent energy wasters
Steam traps are automatic valves that remove air and condensate from steam systems while keeping live steam intact. Their role is critical, yet they are often overlooked in maintenance programs. Statistics reveal that 30% of steam traps fail if not regularly inspected, leading to significant energy losses and potentially damaging equipment. The cost of wasted steam is substantial; repairing just one leaking thermodynamic steam trap can save up to €2,500 annually, while a stuck-open float trap can result in losses exceeding €7,000 per year at higher pressures.
The importance of steam trap monitoring
A malfunctioning steam trap can fail in two ways:
- Failing open: Results in substantial energy loss as live steam is wasted, significantly increasing operating costs.
- Failing closed: Causes condensate to accumulate, reducing system efficiency, leading to water hammer, and possibly damaging equipment.
Using the SDT340 for steam trap monitoring addresses these challenges. Associated with high-quality ultrasound sensors, the SDT340 detects the high-frequency sounds generated by steam trap operation. During operation, steam traps produce distinguishable ultrasound patterns that indicate their condition. The SDT340 captures these patterns, allowing technicians to determine whether a trap is functioning properly or has failed.
- Open trap: Constant ultrasound signal without interruption, indicating the trap is stuck open.
- Closed trap: Little to no sound, showing a failed-closed condition.
By combining ultrasound detection with temperature measurement, the SDT340 allows maintenance teams to quickly assess whether a trap is open or closed, providing immediate feedback for repair decisions. This proactive monitoring not only improves energy efficiency but also reduces costly downtime caused by trap failures.
Predictive maintenance and data integration
The SDT340 goes beyond real-time detection by integrating with Ultranalysis® Suite 3 (UAS3) software, allowing for advanced diagnostics and trend analysis. Technicians can compare the time signal from a suspect steam trap to a reference signal from a functioning trap, making it easier to identify anomalies. This data-driven approach enables predictive maintenance, ensuring that steam traps are repaired or replaced before they fail catastrophically.
Valves: Critical for flow control and safety
Valves, on the other hand, are essential for controlling the flow of liquids and gases in various industrial systems, particularly in oil and gas sectors. Like steam traps, they are prone to failure, which can lead to severe consequences such as production downtime, energy loss, or even safety hazards. Valve failures, particularly leaks, result in the unwanted passage of fluid, reducing system efficiency and potentially compromising safety.
Valves produce distinct ultrasound signatures when they leak or malfunction. A leaking valve generates turbulence as fluid passes through, creating high-frequency sound waves. The SDT340 is designed to detect these ultrasound emissions, enabling technicians to identify valve leaks without dismantling the system. By placing sensors upstream and downstream of the valve, the SDT340 measures and compares ultrasound activity, quickly diagnosing whether the valve is leaking.
- Upstream measurement: Normal sound levels indicate no issue.
- Downstream measurement: Increased sound levels suggest a leak..
This method is not only fast and accurate but also non-invasive, making it ideal for continuous monitoring in environments where dismantling valves for inspection would be time-consuming and costly.
Saving energy and reducing costs
In both steam trap and valve monitoring, the SDT340 enables industries to shift from reactive to predictive maintenance. Instead of waiting for failures to occur, technicians can continuously monitor the health of their equipment, intervening before problems escalate. This proactive approach offers significant advantages:
- Energy savings: Regular steam trap inspections can reduce steam losses by up to 20-30%, translating into thousands of euros saved annually.
- Reduced downtime: Identifying valve leaks or failures early prevents costly production halts and ensures safer operations.
- Improved safety: For industries handling hazardous substances, such as oil and gas, monitoring valve condition is critical for avoiding dangerous leaks.
A smart investment for long-term efficiency
The SDT340 provides industries with a powerful solution for monitoring steam traps and valves, addressing two of the most common sources of energy loss and mechanical failure. By leveraging the sensitivity of ultrasound technology, combined with advanced data analysis through the UAS3 software, the SDT340 enables efficient, non-invasive monitoring that saves both time and money.
Our other news
See allJoin the largest community of industrial suppliers
- Helping you with your ongoing technology watch
- Provide you with detailed supplier statistics
- Give you international visibility
Discover the largest catalogue of industrial products on the market
- To offer you the best catalogue of industrial products on the market
- To guarantee you a 100% secure platform
- Enable you to have live remote exchanges