Early Bearing Fault Detection and Condition Monitoring in Baby Diaper Production Line
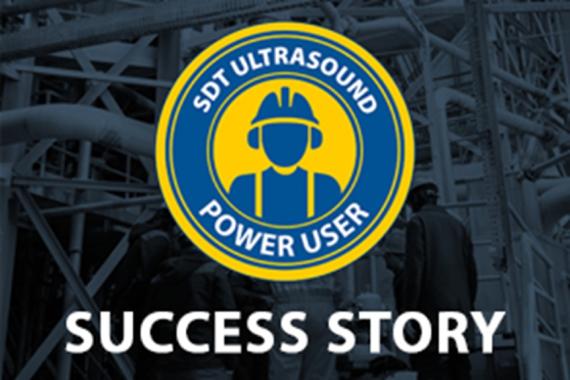
In this project, early bearing fault detection will be performed on two motors in a baby diaper production line using the SDT340 ultrasound device.
The goal is to ensure planned maintenance through early detection of bearing faults, prevent equipment downtime on the production line, and reduce maintenance costs. The condition of the bearings will be analyzed based on measurements and graphical data collected.
1. Project Scope
Inspected Equipment:
- Motor 1: Motor located in the baby diaper production line.
- Motor 2: Motor located in measured together with its fan on the production line.
Technology Used: SDT340 Ultrasound Device
The SDT340 device is used to detect early-stage faults in bearings and monitor lubrication conditions. Compared to vibration analysis, it provides much more sensitive results and allows tracking of fault development.
2. Measurement Process and Data Collection
- Measurement Period: Monthly measurements will be taken on the bearings using the SDT340 ultrasound device. The results will be analyzed each time, and trend changes will be monitored.
- Data Collected: Ultrasound spectrum graphical data and RMS velocity/acceleration values of the bearings. These data will help determine the stage of bearing damage.
3. Review and Interpretation of Graphs
During the evaluation process, the following steps will be taken based on the measurement graphs for each motor:
Motor 1:
- Measurement Locations: Measurements taken from the non-drive end of Motor 1 have been examined.
- Graphs:
- Interpretation: No significant concern was observed in the measurements taken from the motor bearings, but the spectrum of the bearing at the fan pulley side, measured at 78 degrees, shows dominant 1x and 2x signals, indicating a possible misalignment issue. Checking the belt tension, alignment, and bearing axes would be beneficial.
Motor 2 (Fan NDE):
- Measurement Locations: Measurements from the non-drive end, drive end and fan non-drive end of Motor 2 have been examined.
- Graphs:
Motor NDE
Motor NDE
Fan NDE
- Interpretation: The motor body temperature was measured around 75 degrees, and while the vibration values are within acceptable ranges (around 2.5mm/s to 5mm/s), the ultrasound values measured for bearing condition are at warning levels, with dominant signals in the spectrum matching the bearing ball and outer race fault frequencies. In addition, the measurements taken from the fan’s rear bearing suggest an early stage of bearing damage. General motor maintenance and bearing replacement are recommended, while the fan bearing should be monitored with interim measurements.
4. Bearing Fault Analysis and Follow-Up
Analysis Method:
- Interpretation of Peak Frequencies:
- Low-Frequency Peaks: Typically indicate insufficient lubrication or general wear. These vibrations caused by surface friction can be reduced with proper lubrication.
- High-Frequency Peaks: Could be a sign of damage to the bearing’s inner race, balls, or outer race. Depending on the severity of the damage, bearing replacement may be required.
Recommendations:
- For Motor 1: After checking the belt tension, alignment, and bearing axes for the potential misalignment issue, if the peaks increase as the frequency increases, bearing damage may be progressing. It is recommended to re-lubricate the motor and repeat the measurements.
- For Motor 2: If the frequencies are very high and the peaks are large, bearing replacement should be scheduled. The operation of this motor should be monitored and reassessed after further measurements.
5. Monitoring and Maintenance Activities
- Lubrication: Bearings will be lubricated based on the measurement results. The SDT340’s lubrication guide module can be used to add the correct amount of lubricant. Ultrasound measurements will also be conducted during lubrication to observe if the optimal lubrication level is reached.
- Bearing Replacement: If the analysis shows that the bearing damage is irreversible, a planned downtime should be organized for bearing replacement.
6. Conclusion and Reporting
- Condition Monitoring: Through the graphs obtained from the SDT340 measurements, the development of bearing faults was observed, and necessary interventions were planned.
- Early Detection: Bearing faults were detected at an early stage through frequency analysis, preventing costly downtimes.
- Maintenance Strategy: The working life of the equipment was extended through periodic ultrasound measurements and lubrication checks.
7: Calculation of Benefits
- Energy Savings:
Increased Efficiency: Energy consumption is reduced by preventing wear and friction in the bearings. - Maintenance Costs:
Reduced Costs: Early detection and proper lubrication help prevent bearing damage, reducing maintenance costs. - Equipment Life:
Extended Bearing Life: The life of the bearings is prolonged, which reduces the cost of spare parts and labor.
8: Reporting of Return on Investment (ROI)
- Cost Savings:
Within the First 6 Months: Early bearing fault detections using the SDT340 significantly reduced repair costs and downtime, providing a 30% savings in the company’s maintenance costs. - Performance Improvement:
Production Continuity: Bearings and motors operated more smoothly with early fault detection and optimized lubrication. Unexpected downtimes in the production line were reduced by 50%, improving production efficiency. - ROI Calculation:
ROI: When comparing the investments made in the project (device purchase, staff training, analysis processes) with the benefits gained, the return on investment was calculated at 200%. This shows that the capital invested could be recovered within a year.
9: Reporting of Cumulative Assistance
- Achievement of Goals:
Reduction in Bearing Faults: The project’s goal of reducing bearing faults by 80% was successfully achieved with the use of the SDT340. Early bearing faults in the motors and fans were largely prevented, ensuring the continuity of the equipment’s operation. - Reporting of Results:
Management Report: A detailed report was submitted to management, demonstrating the cost savings, production efficiency improvements, and maintenance process optimization achieved through the use of the SDT340 device. The report proved how effective the device was in strengthening the company’s maintenance strategies. - Additional Improvement Suggestions:
Future Steps: Although early detection was successfully achieved, the monitoring and lubrication processes must continue to be optimized. It is also recommended to monitor other equipment with the SDT340.
Conclusion:
The early bearing fault detection project conducted on the production line of a baby diaper manufacturer using the SDT340 device provided significant improvements in the motors and fans. Early detection and proper lubrication strategies extended the equipment’s lifespan, reduced maintenance costs, and increased production efficiency. The project created a major transformation in the company’s overall maintenance processes, ensuring the reliability and sustainability of the production line.
Key Outcomes:
- 80% of bearing faults were detected early and prevented.
- Unexpected production downtimes were reduced by 50%.
- 30% savings were achieved in maintenance costs.
- Return on Investment (ROI) reached 200%.
This project provided the company with a significant cost advantage, improved maintenance processes, and enabled long-term production with fewer breakdowns.
Our other news
See allJoin the largest community of industrial suppliers
- Helping you with your ongoing technology watch
- Provide you with detailed supplier statistics
- Give you international visibility
Discover the largest catalogue of industrial products on the market
- To offer you the best catalogue of industrial products on the market
- To guarantee you a 100% secure platform
- Enable you to have live remote exchanges